
Can Twister with Rinser Line (Twist Conveyor System)
Custom Manufacturing & Installation of Aluminum/Tin Can Conveyor Systems for:
-
Beverage Industry
-
Canning Facilities
-
Food Processing Plants
Key Features:
✓ Direct integration with conveyor lines
✓ Optional built-in rinsing system
✓ Compatibility with standard production equipment
Benefits:
✔ Increased production efficiency
✔ Precise can positioning
✔ Reduced manual labor
✔ Full compliance with industry standards
Technical Capabilities:
-
Handles all standard aluminum/tin can sizes
-
Custom solutions for your production parameters
-
Quick installation on existing equipment
Can Rinsing Systems - Guaranteed Hygiene and Compliance
In high-speed production lines, proper rotation and orientation of tin cans are critical to prevent costly errors and ensure uninterrupted operations. Kasar Makine (KM) specializes in custom-designed can twisting and turning systems tailored to each customer's needs. Our solutions provide flawless rotation and precise positioning on conveyor belts, maximizing production efficiency and accuracy.
Key Benefits of KM Can Rinser Systems
✔ High Efficiency – Automated cleaning reduces manual labor and boosts productivity.
✔ Waste Reduction – Innovative washing technology minimizes water and energy consumption.
✔ Product Integrity – Gentle yet effective cleaning prevents contamination and can damage.
✔ Regulatory Compliance – Meets strict hygiene standards for the food and beverage industry.
✔ High-Speed Performance – Processes up to 2,000 cans per minute without compromising quality.
Why Choose KM Twist & Rinse Systems?
✓ Smart Automation – Autonomous washing systems eliminate operator intervention.
✓ Eco-Efficiency – Water-saving technology reduces consumption by up to 40%.
✓ Precision Cleaning – Zero-damage guarantee with non-stop operation.
✓ Full Compliance – Adheres to global hygiene standards (FDA, EHEDG, etc.).
✓ High Capacity – Industry-leading speed of 2,000 cans/minute with consistent performance.
✓ Custom Solutions – Tailored to fit seamlessly into your production line.
OUR TWIST AND RINSER
PROJECTS
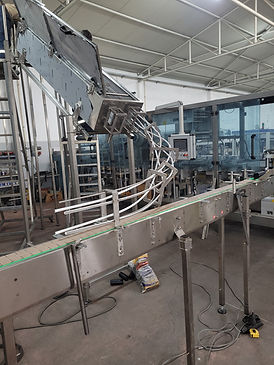


Carlsberg
/ Kazakhstan
High-Speed Can Twist & Rinse Line for Beverage Production
Designed for 250ml Aluminum/Tin Cans
Industry-leading capacity: 70,000 cans per hour
Integrated twisting and rinsing technology for beverage facilities
Custom-engineered can handling solutions
Key Features:
✔ Precision Twist Mechanism – Ensures accurate can orientation
✔ High-Efficiency Rinsing – Meets food-grade hygiene standards
✔ Heavy-Duty Construction – 24/7 continuous operation
✔ Smart Conveyor Integration – Seamless production line synchronization
Technical Specifications:
• Capacity: 70,000 cans/hour (1,166 cans/minute)
• Can Sizes: 250ml (custom sizes available)
• Materials: Food-grade stainless steel contact surfaces
Pepsi Co
/ Kazakhstan
3-Lane Can Twister & Rinser System - Custom Solution for Beverage Industry
Parallel processing for 500ml, 330ml & 250ml tin/aluminum cans
Industry-standard capacity: 35,000 cans per hour
(3 parallel lanes)
Integrated twisting and rinsing technology for beverage facilities
Custom-engineered can handling solutions
Key Features:
✔ Multi-Lane System - Handles 3 different can sizes simultaneously
✔ Precision Twist Mechanism - Ensures accurate can orientation
✔ High-Efficiency Rinsing - Food-grade cleaning performance
✔ Robust Construction - 24/7 continuous operation capability
✔ Smart Conveyor Integration - Seamless production line compatibility
Technical Specifications:
• Capacity: 35,000 cans/hour (583 cans/minute)
• Can Sizes: 500ml, 330ml, 250ml (customizable)
• Materials: Stainless steel contact surfaces